अनभूले पैठणी येवला
India is well known since ancient times for its handloom and cloth weaving industry. One of the major trade items in the Indo-Roman trade in the 2nd century CE was woven cloth, especially muslin, a cloth that can be dyed and embroidered, originating from Paithan. Caves in the region, from 1st century BCE to the 3rd Century CE, display inscriptions which detail the weaving industry of this era (Ministry of Textiles, GoI, 2008). Cotton and silks woven in India were one of the principal trade items until the 20th century CE, with brocades, fine cotton and linen being exported along with spices and other items. The Paithani, originating from Paithan, is one such handloom treasure purely woven in silk and zari (thread made of gold or silver).
Trade records from the 2nd century BCE maintain mentions of the silks and cotton of Pratishthana (Paithan) being exchanged for Roman wines and olive oil. Paithan has thus been a flourishing trade and textile town since the 2nd century BCE, however the craft of the Paithani really flourished in the 17th century and further reached its zenith in the early 19th century before witnessing a slow decline over time till it was revived in the 1960s and 1970s.
Crafts and other arts in India follow a specific pattern of transfer of knowledge from generation to generation. The art of weaving the Paithani follows a similar pattern with the art staying within the family. A master weaver would have apprentices from his family and total devotion to the craft was necessary with the tools of the trade being considered as a manifestation of god. Guilds of weavers were established for managing and ensuring creative competition and guaranteeing employment.
Today’s Paithani weavers are no longer from the original weaving families of Paithan and are specially trained in a Government of Maharashtra initiative workshop. Several private traders have established workshops as well with weavers from different places, especially southern India. The ancillary activities of weaving, such as zari making, dyeing or silk preparation, have all but disappeared from Paithan.
The Paithani, a pure silk saree with a zari of gold and silver traces its origin to the brocades of the Yadavas which were sourced from Paithan. Several descriptions of these brocades are traced including Ganga varni (in the shades of the Ganga), Bora jail (brocades with sprigs of flowers) and Malganthi, a textured fabric popular in the Yadava Empire.
The traditional Paithani saree is manufactured by hand in pure silk and dyed in traditional colours. Silk was originally sourced from Bangalore or Mysore and zari was sourced from various places in Gujarat, especially Surat. The preparation of silk and zari, dyeing and weaving, was all carried out in Paithan with its traders establishing guilds for the weaving of sarees. This range of ancillary activities also influenced the urban form of Paithan.
Components of a Paithani
A typical saree consists of a set of components such as the body, decorative edge (padar) and borders (zari kath). The Paithani is identified by its characteristic kath and padar which have typical motifs. These motifs are an important part of identifying the Paithani. Several types and variations of these motifs exist.
The components of the Paithani are:
The body (saree cha aanga) – The plain or decorated fabric which is the major component of the saree and woven in silk with small buttis. The buttis maybe of varying designs. The total length of the saree may be ‘sahavari’ or ‘nauvari’ with a varbeing equivalent to a yard of fabric. The typical Paithani is hence either six yards or nine yards in length and the width including the zar is one panna or 44 inches.
The edge (kath) – The border of the saree is in zari to add stiffness to the fabric and protect its edges from wear and tear. This is known as the kath. The kath is intricately decorated with traditional motifs and varies in thickness from two inches to 12 inches based on the skill of the weaver and design chosen for the saree. The kath is along both edges of the body of the saree and is designed symmetrically. It terminates into the padar and uses similar designs, motifs and colours.
The pallu (padar) – The Paithani padar has its own unique design. It generally consists of motifs of peacocks, flowers and leaves. The padar is generally about 24 to 36 inches of intricately woven zariwork at one end of the saree and hangs free over the left shoulder once the saree is draped.
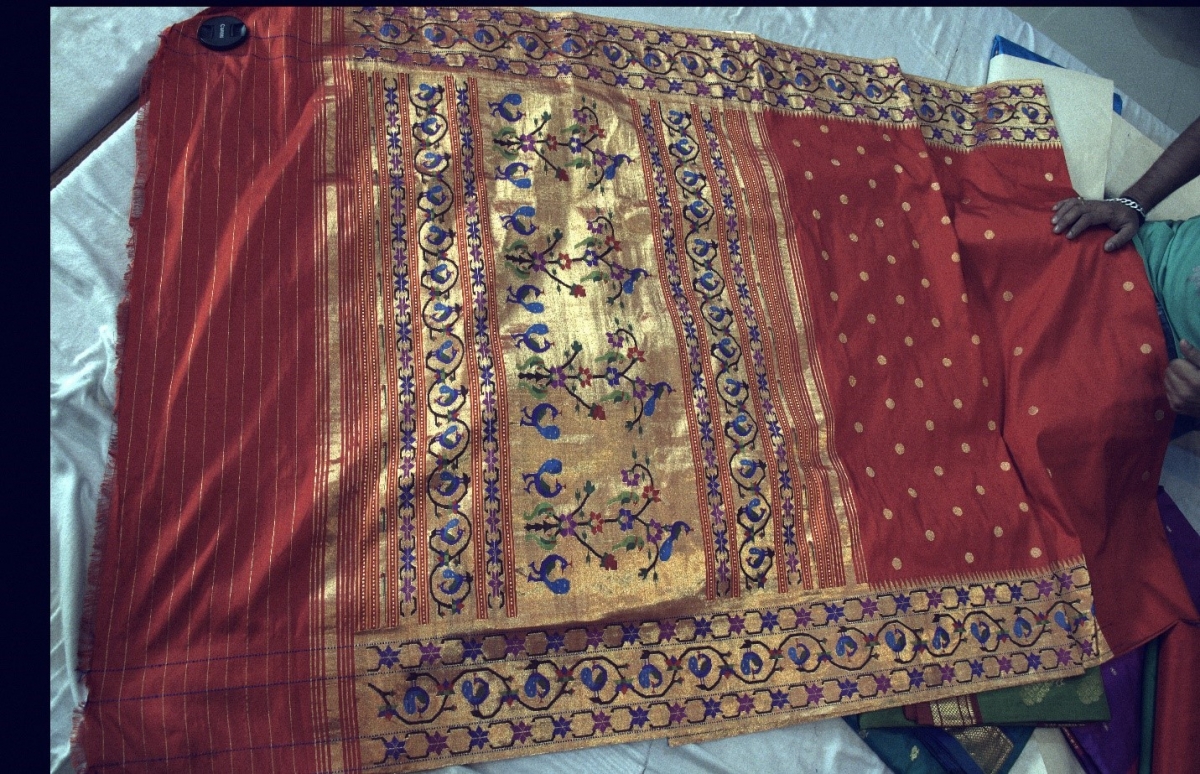
Figure 1. Components of a Paithani saree
The total weight of a finished Paithani varies from 900 gm to 1500 gm depending on the quality of silk and zari used as well as width, quality and work required on the kath and padar.
Raw materials of the Paithani
The Paithani consists of two simple raw materials— mulberry silk historically and presently sourced from Bengaluru and Mysore, and zari, sourced from Surat, Gujarat.
Mulberry Silk
The silk was historically sourced from Mysore and Bengaluru. Mulberry silk was preferred for weaving. The undyed and unsorted silk was imported to Paithan and later dyed with organic dyes at the dyers' settlement to the south of Paithan. Today, the silk is generally pre-dyed with chemical dyes and obtained in two varieties. The warp (tana) is pre-stretched and is bought with pre-counted threads and in the length required for two sarees. The weft (bana) is brought as single filaments of silk and twirled together four or five times depending on the thickness of silk cloth to be woven before starting the weaving process. Silk is obtained in kilograms with mulberry silk costing around Rs. 3000 to Rs. 4000 per kilo. Each saree requires about 700 to 800 grams of silk thread for both tana and bana considering loss during weaving. Silk is tested for quality and authenticity by burning a length of silk. The silk thread after burning should smell like burnt hair and crumple into a ball which breaks easily after touching.
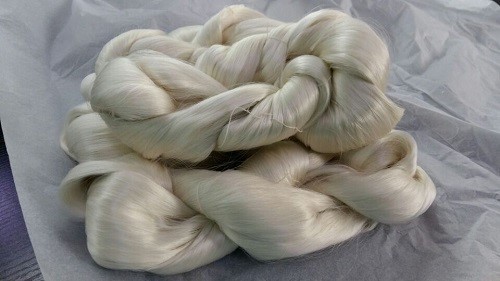
Figure 2. Undyed mulberry silk yarn. Source: www.indiamart.com/karmaenterprisesrajkot/Dinesh Bhai Patolawala Shop.
Zari
These days the zari is obtained from Surat. Zari is available in two types, copper zari which is a cotton thread twirled with copper wire and wrapped in gold foil, and silver zari, which is a silver wire with cotton thread coated with gold foil. The copper zari is cheaper and easier to weave and hence preferred over the silver zari. The market rate of zari varies everyday with copper zari costing around Rs. 2000 to Rs. 4000 per kilo based on the percentage of gold used, and silver zari costing Rs. 5000 to Rs. 6000 per kilo; each saree requires arounf 100 to 250 grams of zari.
Silver zari was traditionally used twirled with saffron or yellow cotton thread. The silver used was often mixed with zinc to impart strength and then coated with gold. Historically, embroidery of the kath-padar is done by a combination of gold and silver zari. The proportion of gold and silver is approximately one is to five to achieve the required strength of the zari. The ratio of silver to gold in the zari varies and the names of the saree evolved from these variations. As gold is measured in masa the names of the saree are described as chouda masi, bara masi and athara masi or eksheri, pavsheri or tinsheri, etc., denoting the amount of gold used. A shera is roughly hundred grams of zari.
The value of the Paithani is dependent on the amount of silver and gold zari used in it. Once the silk starts to tear, the saree is burnt down to extract the silver. However, this is not possible in sarees with copper zari. The test to check the presence of silver in the zari is to burn a single thread. In case of silver being present, the zari thread turns white and upon rubbing with hands, the silver wire is exposed. In case of copper being present, the remnants turn reddish black.
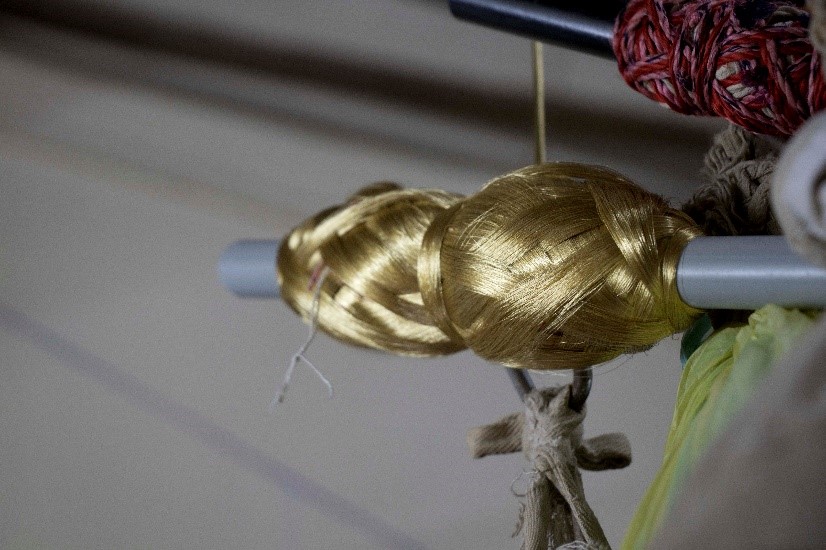
Figure 3. Silver-based zari used for weaving kath and padar
Dyes
Originally organic dyes were used for dyeing the silk. The dyes were obtained from various roots, flowers and metal oxides. The natural dyeing process is as follows: the unbleached silk is boiled in a solution of sodium carbonate or chuna (lime powder) or papad khar (sodium bicarbonate). This bleached silk is then soaked overnight in cold water and alum solution to act as a mordant. Mordant is required to ensure that the colour holds and does not bleed.The dye is added to boiling water and the bleached silk is soaked in the water for over an hour. This causes the dye to seep into the silk fibres and hold. This process is repeated multiple times till the required depth of colour is obtained.
Traditionally used colours such as deep yellow (pophali) is obtained from turmeric root and light yellow obtained from marigold flower petals. Deep yellow and orange colour is obtained from papad khar (sodium bicarbonate) and kapila(mallotus philippensis) powder. Kachi hirva or bottle green is from leaves of the gulmohar. Saffron is mixed with turmeric and the noni plant to obtain a deep mango yellow colour with alum as a mordant. Lavender and shades of blue are obtained by combining indigo with various other dyes such as red and black. Deep reds and magenta colours (falsa) are obtained by using Acacia arbica and Arabica catechu tree parts.
Plants used for obtaining dyes, which are commonly found in the Marathwada region are listed below. Various parts of the plants are used to obtain dyes. These names have been verified through research as well as through traditional knowledge bases of the weavers (Sujata Saxena 2014; Bhute 2012).
No comments:
Post a Comment